1.Why do silicone molds have fewer flipping times?
Too much silicone oil was added during the mold making process, which damaged the molecular weight of the silicone oil. As a result, the mold may have fewer flips and become less durable. If we use high hardness silicone to mold small products with complex patterns, there will be fewer mold flips because the silicone will be brittle and prone to breakage when it is hard for a long time.
On the contrary, if silicone with low hardness is used to make molds for building products, the result will also be unsatisfactory. Because silicone is too soft, its tensile and tear strength will decrease, and the resulting mold will deform, resulting in a decrease in the number of mold flips. The quality of the mold adhesive itself is very good, and there is no distinction between good and bad silicone, only suitability and unsuitability. We need to use silicone that is suitable for the hardness of the product to make the mold, so that this situation will not occur.
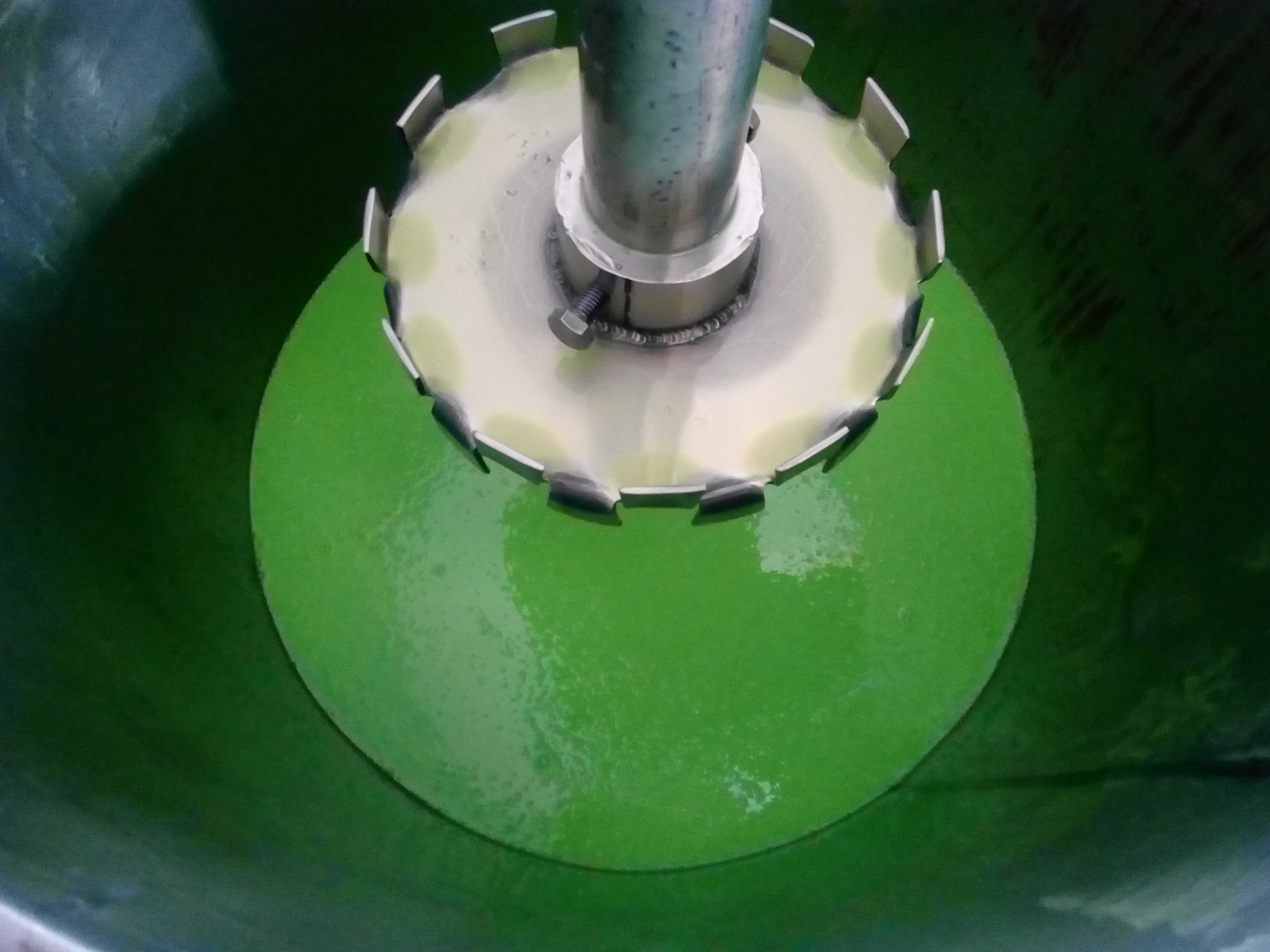
2.Why does silicone mold burn out?
Due to the addition of peroxide curing agents to unsaturated resins and resin products, a large amount of heat is generated when the resin reacts. Generally, the resin curing time is 3 minutes, so it is necessary to demold as soon as possible after 3 minutes to prevent the silicone mold from burning out.
3. Methods for making silicone injection molds and slicing molds:
Splitting mold or sheet mold operation method: Apply the evacuated silicone by brushing or pouring. If you are making sheet molds or dividing molds and use brushing method, before brushing, apply a layer of release agent or isolation agent to the product or model you want to replicate, and then brush the silicone on the product (note: be sure to brush evenly).
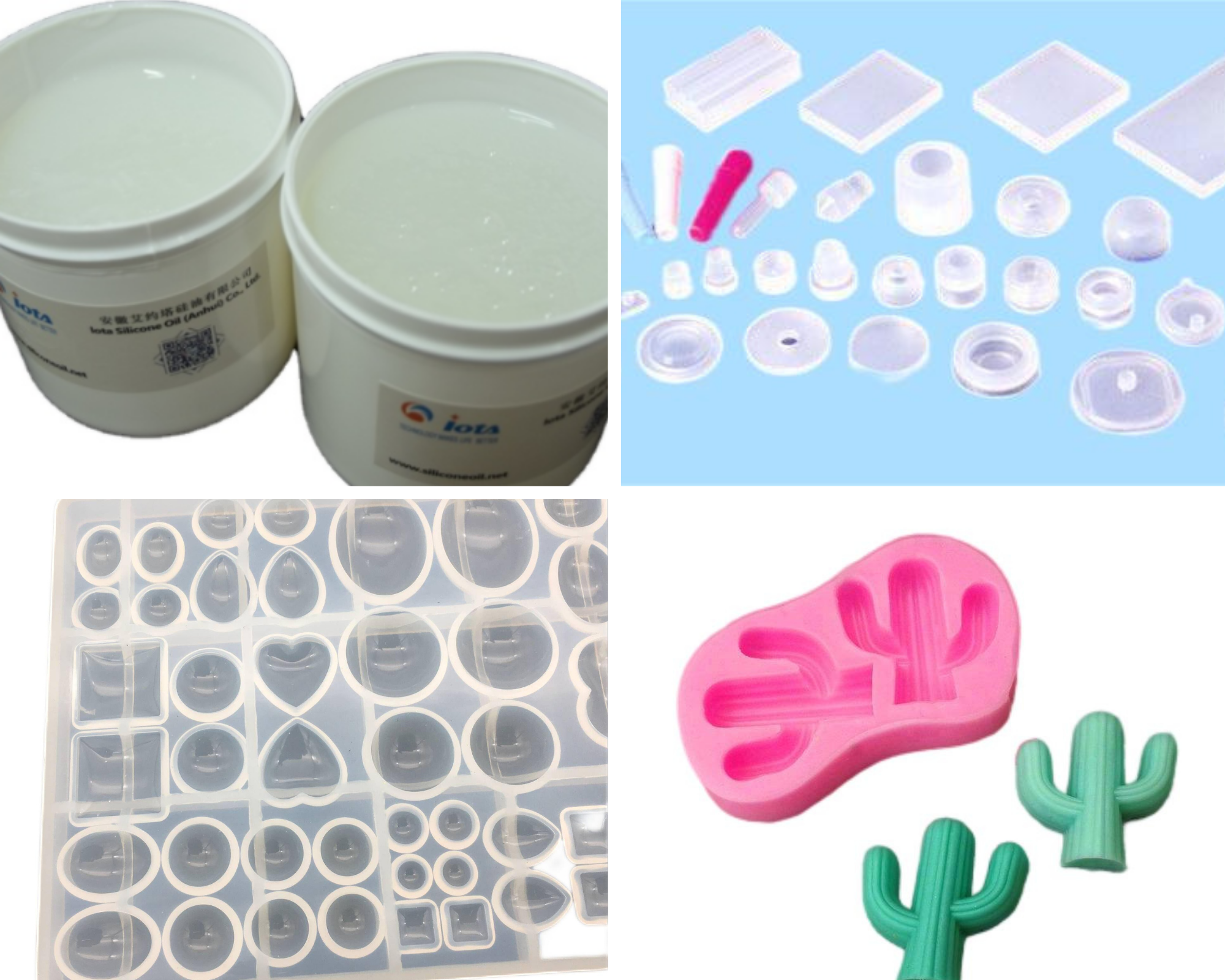
Wait for 30 minutes, then stick a layer of gauze or fiberglass cloth on the surface to increase strength, and then apply a second layer of silicone. After the silicone dries, make the outer mold. The outer mold can be made of materials such as gypsum or resin.
4. The operation method of injection molding or pouring mold: Injection molding or pouring mold is used for relatively smooth or simple products. It is to enclose the product or model you want to replicate with a rubber plate or glass plate, and pour the evacuated silicone directly onto the product.
After the silicone is dried and formed, the product is taken out, and the mold is formed (note: injection mold generally uses silicone with relatively soft hardness to make the mold, which makes demolding easier and will not damage the products inside the silicone mold). The above is the entire process of using and operating the silicone mold.
5.Why does the silicone mold appear to be dry on the surface but not dry on the inside?
Mold silicone belongs to the condensation type silicone gel, which solidifies by absorbing moisture from the air. During the production process of silicone gel, the moisture is evaporated without adding an appropriate amount of moisture, resulting in this phenomenon.
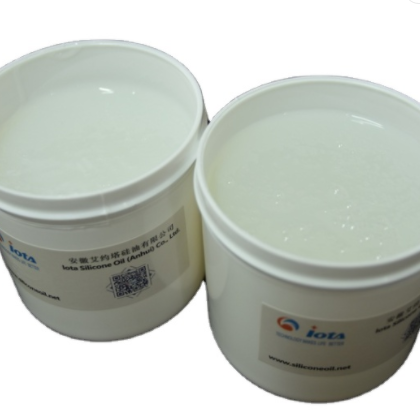
Solution: This phenomenon is not a product quality issue, but rather due to the failure to control moisture and improve the storage life of silicone. The phenomenon only occurs when the shelf life is long. As long as 0.05% moisture is added appropriately and stirred evenly when using silicone, some problems can be solved.
About injection liquid silicone rubber,please check the details: H
igh Strengh Liquid Silicone Rubber IOTA 28-Series
About fluorosilicone rubber,please check the details: Fluoro Silicone Gum (IOTA 110-F series)
About ethyl silicone oil,please check the details:
Polyethylsiloxane Fluids IOTA 2056 PES
About leather silicone rubber,please check :
IOTA Liquid silicone rubber for silicone leather